Jabsco 31820-0492 Bedienungsanleitung
Lesen Sie kostenlos die đź“– deutsche Bedienungsanleitung fĂĽr Jabsco 31820-0492 (4 Seiten) in der Kategorie pomp. Dieser Bedienungsanleitung war fĂĽr 19 Personen hilfreich und wurde von 2 Benutzern mit durchschnittlich 4.5 Sternen bewertet
Seite 1/4
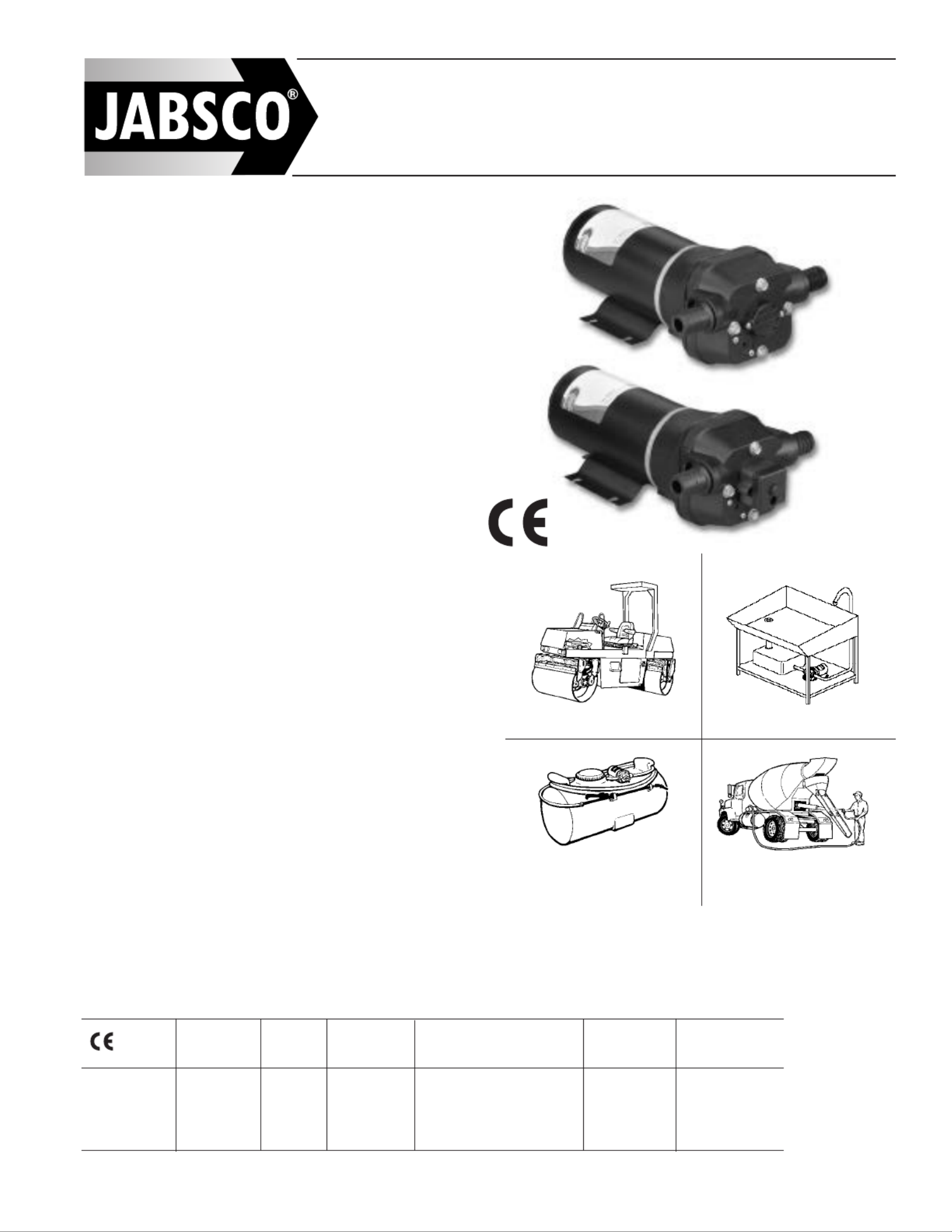
Models 31820,31821 Series
NOTE: Viton equipped models are not suitable
for potable water applications.
* Viton is a registered trademark of DuPont Dow Elastomers L.L.C.
** Santoprene is a registered trademark of Monsanto.
Construction Equipment
Washdown
Spray Equipment
Road Rollers Parts Washing
FEATURES
•Sealless
•Run Dry Ability
•Self-Priming
•Thermal Overload Protected Motor
•Corrosion Protected Motor
•Snap-in 1/2"(13 mm) Dia. Port Adaptors
•Conforms to Electromagnetic Compatibility 89/336/EEC and
Machinery Directive 89/392/EEC, EN50081-1
•Easy Installation
•Flow to 3 GPM/12 LPM
•Low Amp Draw
•Compact Size
•Quiet Running
INDUSTRIAL DIAPHRAGM PUMPS
Commercial Duty, 3 GPM/12 LPM
31820-0492 3 (12) 12 Vdc YES N/A N/A 5 15
31820-0494 3 (12) 24 Vdc YES N/A N/A 2.5 7.5
31821-0492 3 (12) 12 Vdc YES 25 (1.7) 40 (2.8) 5 15
31821-0494 3 (12) 24 Vdc YES 25 (1.7) 40 (2.8) 2.5 7.5
Protective Pressure Switch Settings Recommended
Models Flow Coated Nominal psi (bar) AMP Draw Fuse/Breaker
GPM (LPM) Voltage Motor Cut-In Cut-Out @ 10 psi Sizes
SPECIFICATIONS
Pump Body: Glass Filled Polypropylene
Elastomers: Santoprene** Diaphragm, Valves of Viton*
Hardware: Stainless Steel
Pump Design: Multi-Chamber Diaphragm
Suction Lift: Self-Priming to 10 ft (3 m) (wet)
5 ft (1.5 m) (dry) min.
Duty Cycle: Continuous, Maximum 40 psi (2.8 bar) at
Ambient of 130° F (54.4° C)
Ports: 1/2 (13 mm)"(13 mm) Hose Barb and 1/2"
Straight Pipe Thread
Motor: Permanent Magnet with Thermal
Overload Protection
Temperature: Liquid temperature range is 45°F (7°C)
to 130°F (54.4°C)
Viscosity: 250 centipoise maximum
Shipping Weight: 7 lb (3.2 kg) approx. (12/24 V models)
APPLICATIONS
This pump provides excellent service in the following
applications.
CONSTRUCTION: Water supply pump to the spray bars
of road rollers and other compaction equipment, street
sweepers, and truck mounted dust control systems.
AGRICULTURAL: Supply pump for herbicide and pesti-
cide spraying equipment.
INDUSTRIAL: Fluid transfer applications for mild acids
and bases. Chemical feed pump. Washing fluid supply
pump in parts washing systems. Machine coolant pump.
Concrete saw lubricant supply pump. Recirculating
pump in filtering systems.
Models 31820-Series
31821-Series
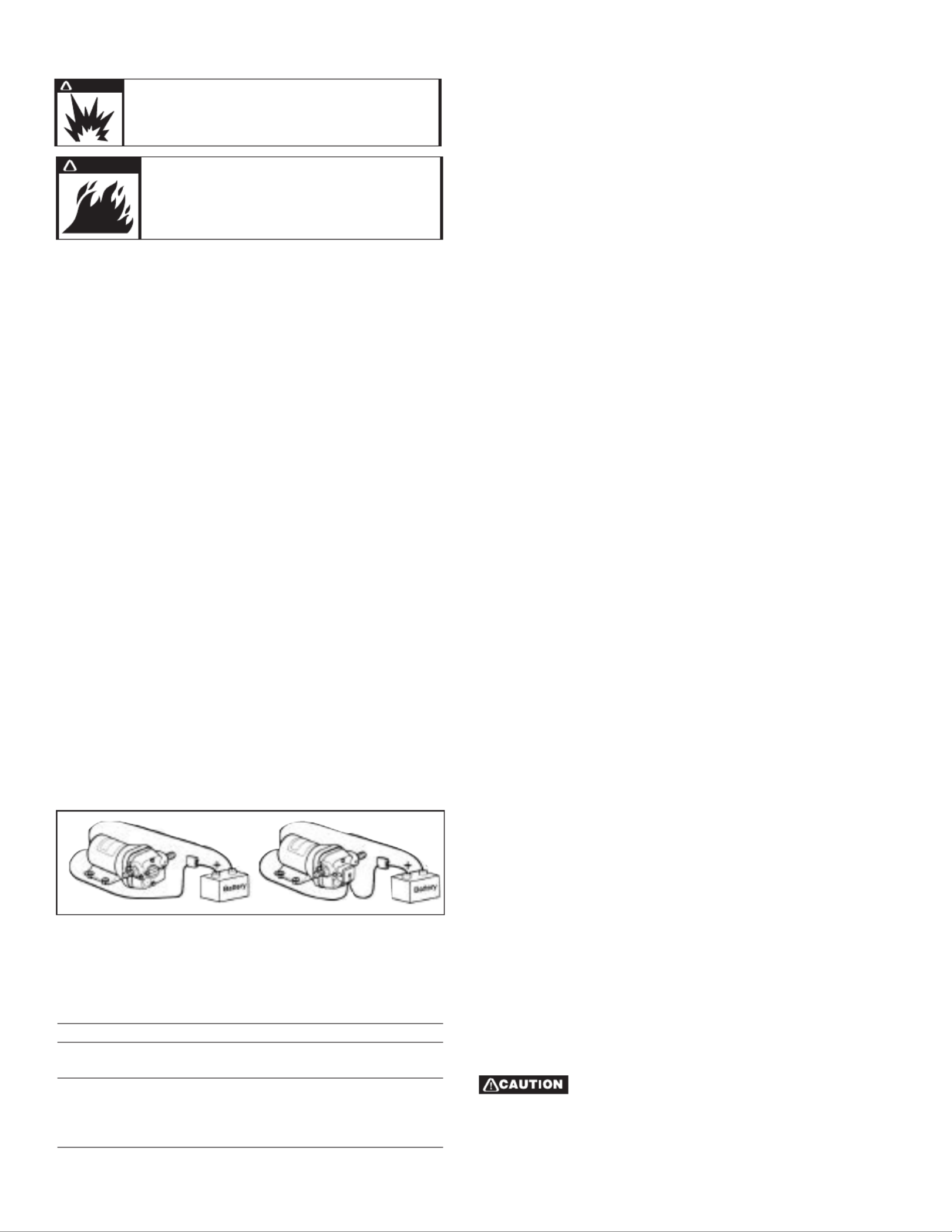
OPERATING INSTRUCTIONS
1. MOUNTING – JABSCO diaphragm pumps are self-
priming and may be located in a dry location above or
below the uid supply. To vertically mount these units,
it is best to do so with the motor on top. This will prevent
fluid dripping on the motor in the event of a leak. Place
pump on a solid surface and secure with four mounting
screws being careful not to fully compress the rubber
grommets which act as shock absorbers.
2. PLUMBING – Port adaptors are supplied to fit
1/2"(13 mm) dia. ID hose or 1/2"(13 mm) dia. straight
pipe threads. Use Teon* (PTFE) type tape when
threading straight pipe threads to tapered pipe threads.
Select two of the port adaptors supplied to match
your plumbing system. Flexible hose or tubing is
recommended instead of rigid piping at pump.
If you choose to use rigid piping, provide a short length
of hose between pipe and the pump to avoid noise and
vibration. Use clamps at both ends of hose to prevent
air leaks. NOTE: Intake hose should be at least
1/2"(13 mm) ID reinforced hose.
A “Pumpgard” 36400-Series 1/2"(13 mm) or 36200-
Series 3/4"(19 mm) in-line strainer should be installed
between pump and fluid supply to keep debris out of
system. Avoid any kinks or ttings which could cause
excessive restrictions. Remember to periodically clean
“Pumpgard” screens.
3. WIRING DC MODELS – In an easily accessible
location, install an “on-off” switch (Jabsco 44960-Series)
to control electricity to the pump. Turn the pump o
when not used for extended periods, or when fluid
supply is depleted.
Select wire size from chart below. Use total length of
wire from electrical source to pump and return. Chart
allows for 3% voltage drop. If in doubt, use next larger
wire size.
RECOMMENDED WIRE SIZES
Total Wire Length – feet (meters)
Pump 0-20 20-35 35-55
Voltage (0-6) (6-11) (11-17)
12 Volt #14 AWG #12 AWG #10 AWG
(2.5 mm2) (4 mm2) (6 mm2)
24 Volt #16 AWG #14 AWG #12 AWG
(1.5 mm2) (2.5 mm2) (4 mm2)
The electrical circuit should be protected with an over-
current protection device in the positive lead. See chart for
proper size. The pump circuit should not include any other
electrical loads. Black Wire from the motor is negative,
orange is positive.
If you are not familiar with applicable electrical standards,
have the unit installed by a qualified electrician.
After installation, check the voltage at the pump motor.
Voltage should be checked when pump is operating. Full
voltage must be available at the pump motor at all times.
4. SELF-PRIMING – Pump is self-priming. Vertical dry
lift capacity is 10 ft (3 m) (wet) 5 ft (1.5 m) (dry) min.
Be sure suction piping is airtight or pump will not
self-prime.
5. RUNNING DRY – Pump can run dry indefinitely without
damage.
6. CHEMICAL COMPATIBILITY – Fluids being pumped
must be compatible with the materials of construction.
Consult factory for Chemical Compatibility Guide. Pump
should be flushed with clean water or neutralizing
solution after each use to prolong pump life.
7. PRESSURE – Maximum continuous duty discharge
pressure is 40 psi with an ambient temperature no
greater than 130°F (55°C).
NOTE: If the system operating pressure exceeds
50 psi, an external pressure relief value should be
installed in the system.
8. TEMPERATURE – The maximum recommended fluid
temperature is 130°F (54°C). Minimum recommended
uid temperature is 45°F (7°C).
9. VISCOSITY – The maximum pumped fluid viscosity is
250 centipoise.
10. DUTY CYCLE – Motor and pump are designed for
continuous operation in a 130°F (55°C) environment
while pumping against 40 psi (2.8 bar) discharge
pressure. Beyond these parameters, an intermitted
duty cycle is recommended to maximize pump life. In
normal operation, motor case will get hot. Prolonged
contact with motor could cause a burn on human skin.
11. START-UP AND OPERATION – Check level of fluid in
supply tank. Open all valves in system. Switch pump
electrical circuit to “on” position. Flow will become
steady as air is bled from system. For pumps equipped
with pressure switch, close discharge valve after flow
becomes steady fluid stream. Pump should shut off
soon after closing valve. Pump is now ready for
automatic operation. Pump will start when valve is
opened and stop upon closure of valve. If pump is to
be inoperative for a considerable period of time, flush
pump with water, turn off electrical circuit to pump, and
bleed system pressure by opening discharge valve.
Pumps have thermal overload protected
motors. The motor will automatically shut off as temper-
ature rises due to an overload condition. If the motor
shuts o in this manner, turn o electrical supply to
pump. After a cooling o period, re-start pump.
Black
Orange
Black
Orange
Explosion hazard. Do not pump gasoline or 
other flammable liquids. To do so can cause 
an explosion resulting in injury or death.
WARNING
!
* TEFLON is a registered trademark of E.I. DuPont de Nemours and Company.
WARNING
!
Fire hazard. Wiring must comply with
applicable electrical standards and include
a properly sized fuse or circuit breaker.
Improper wiring can cause a re resulting
in injury or death.
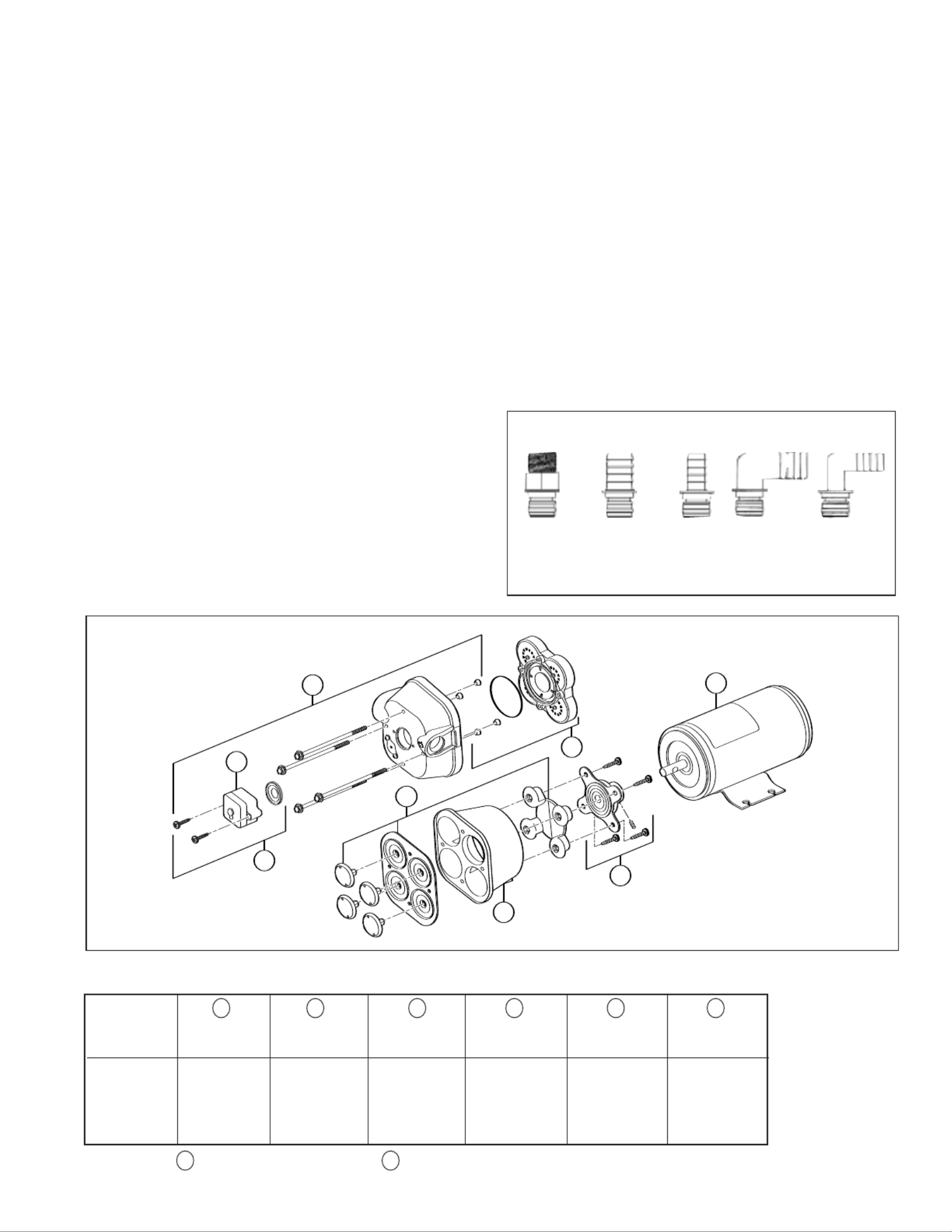
2
7
4
8
3
15
6
EXPLODED VIEW
8. Check that ferrules are installed in upper housing and
O-ring is properly seated.
9. Install check valve assembly in upper housing and t
upper and lower housings together.
10. Align pumphead with motor and tighten four (4) screws
evenly using 25 inch pounds (2.8 Nm) of torque.
SWITCH REPLACEMENT
1. Remove power from pump. Relieve system pressure.
Disconnect inlet and outlet hoses.
2. Remove pressure switch cover and disconnect power
leads from switch.
3. Remove switch and switch diaphragm from pump by
removing two (2) switch mounting screws.
4. Replace switch diaphragm and switch. Reassemble in
reverse order.
5. Do not over tighten switch mounting screws.
OPTIONAL PORT KITS
30649-1004
1/2"Threaded
EPDM
30642-1004
90° - 3/4"
Hose Barb
Viton
30651-1004
90° - 1/2"
Hose Barb
Viton
SERVICE INSTRUCTIONS
PUMP DISASSEMBLY
1. Remove power from pump. Open discharge valve to
relieve system pressure.
2. Push port clips back and disconnect plumbing from
pump.
3. Remove the four (4) pumphead screws.
4. Rotate pumphead until cam/bearing set screw is visible
through drain notch.
5. Loosen cam/bearing set screw and slide pump o
motor shaft.
6. Separate upper housing, lower housing, and check
valve assembly as required.
PUMP ASSEMBLY
1. Install new outer piston in lower housing with piston
tops pointing away from motor.
2. Install new diaphragm in lower housing with the
molded O-ring seals facing away from motor.
3. Insert each inner piston through the diaphragm into
outer piston.
4. Turn each piston until fully seated.
5. Secure cam/bearing assembly to outer pistons using
18 inch pounds (2.0 Nm) of torque.
6. Slide lower housing on motor shaft. Align set screw
with motor shaft indentation.
7. Set screw MUST be positioned over shaft indentation
and secured tightly.
PARTS LIST
Model Upper Check Diaphragm Cam/Bearing PressureMotor
Housing Kit Valve Kit Kit Kit Kit Switch Kit
31820-0492 18910-4019 18911-7020 18912-3040 18913-0002 18919-0116 —
31820-0494 18910-4019 18911-7020 18912-3040 18913-0002 18919-1040 —
31821-0492 18910-4007 18911-7020 18912-3040 18913-0002 18919-0116 18916-0118
31821-0494 18910-4007 18911-7020 18912-3040 18913-0002 18919-1040 18916-0118
Bearing cover 7 not included in diaphragm Kit 3 .
1 2 3 4 5 6
Port Kits contain two ports with O-rings
30653-1004
3/4"Straight
Hose Barb
Viton
30654-1004
1/2"Straight
Hose Barb
Viton
Produktspezifikationen
Marke: | Jabsco |
Kategorie: | pomp |
Modell: | 31820-0492 |
Brauchst du Hilfe?
Wenn Sie Hilfe mit Jabsco 31820-0492 benötigen, stellen Sie unten eine Frage und andere Benutzer werden Ihnen antworten
Bedienungsanleitung pomp Jabsco

13 August 2024

11 August 2024

6 August 2024

5 August 2024
Bedienungsanleitung pomp
- pomp Crivit
- pomp SilverCrest
- pomp SKS
- pomp Makita
- pomp Vonroc
- pomp Siemens
- pomp Powerfix
- pomp Black And Decker
- pomp Ryobi
- pomp Coleman
- pomp Einhell
- pomp Worx
- pomp Bartscher
- pomp Ultimate Speed
- pomp Eheim
- pomp Eurom
- pomp Hyundai
- pomp Fuxtec
- pomp Hazet
- pomp Metabo
- pomp Kärcher
- pomp GĂĽde
- pomp Scheppach
- pomp Fieldmann
- pomp Wetelux
- pomp Westfalia
- pomp Vaillant
- pomp Husqvarna
- pomp Enermax
- pomp MSW
- pomp Germania
- pomp Fluval
- pomp Vetus
- pomp Sanibroyeur
- pomp Topeak
- pomp Hayward
- pomp Gre
- pomp Milwaukee
- pomp Toolcraft
- pomp Osram
- pomp Bestway
- pomp AL-KO
- pomp Gardena
- pomp Melinera
- pomp Powerplus
- pomp Blackburn
- pomp Lezyne
- pomp Alpha Tools
- pomp Sicce
- pomp Bulex
- pomp Danfoss
- pomp Comet
- pomp Hozelock
- pomp Ozito
- pomp Blumfeldt
- pomp Nibe
- pomp Sun Joe
- pomp Fluke
- pomp Nefit
- pomp Oase
- pomp POLARIS
- pomp Velda
- pomp Vivaria
- pomp Waldbeck
- pomp WHALE
- pomp AstralPool
- pomp Pedrollo
- pomp Esotec
- pomp T.I.P.
- pomp Panduit
- pomp Heissner
- pomp DAB
- pomp Abac
- pomp Baracuda
- pomp Ubbink
- pomp JANDY
- pomp Liberty Pumps
- pomp Monzana
- pomp Lifan
- pomp Elpumps
- pomp For_Q
- pomp Simpson
- pomp Pontec
- pomp BluGarda
- pomp Grundfos
- pomp Zoeller
- pomp B-Air
- pomp Anova
- pomp Perlick
- pomp Fiap
- pomp Little Giant
- pomp Ebara
- pomp Basement Watchdog
- pomp Barwig
- pomp Wayne
- pomp Ribimex
- pomp Maruyama
- pomp ESPA
- pomp Hollex
- pomp Sauermann
- pomp Eco-Flo
- pomp Nowax
- pomp EvoHeat
- pomp Zéfal
- pomp OSIP
- pomp Franklin Electric
Neueste Bedienungsanleitung fĂĽr -Kategorien-

16 Oktober 2024

16 Oktober 2024

16 Oktober 2024

15 Oktober 2024

15 Oktober 2024

15 Oktober 2024

13 Oktober 2024

7 Oktober 2024

2 Oktober 2024

1 Oktober 2024