Vivax HPP-24CH70AERI R32-1 Bedienungsanleitung
Vivax
Wärmepumpe
HPP-24CH70AERI R32-1
Lesen Sie kostenlos die 📖 deutsche Bedienungsanleitung für Vivax HPP-24CH70AERI R32-1 (56 Seiten) in der Kategorie Wärmepumpe. Dieser Bedienungsanleitung war für 19 Personen hilfreich und wurde von 2 Benutzern mit durchschnittlich 4.5 Sternen bewertet
Seite 1/56
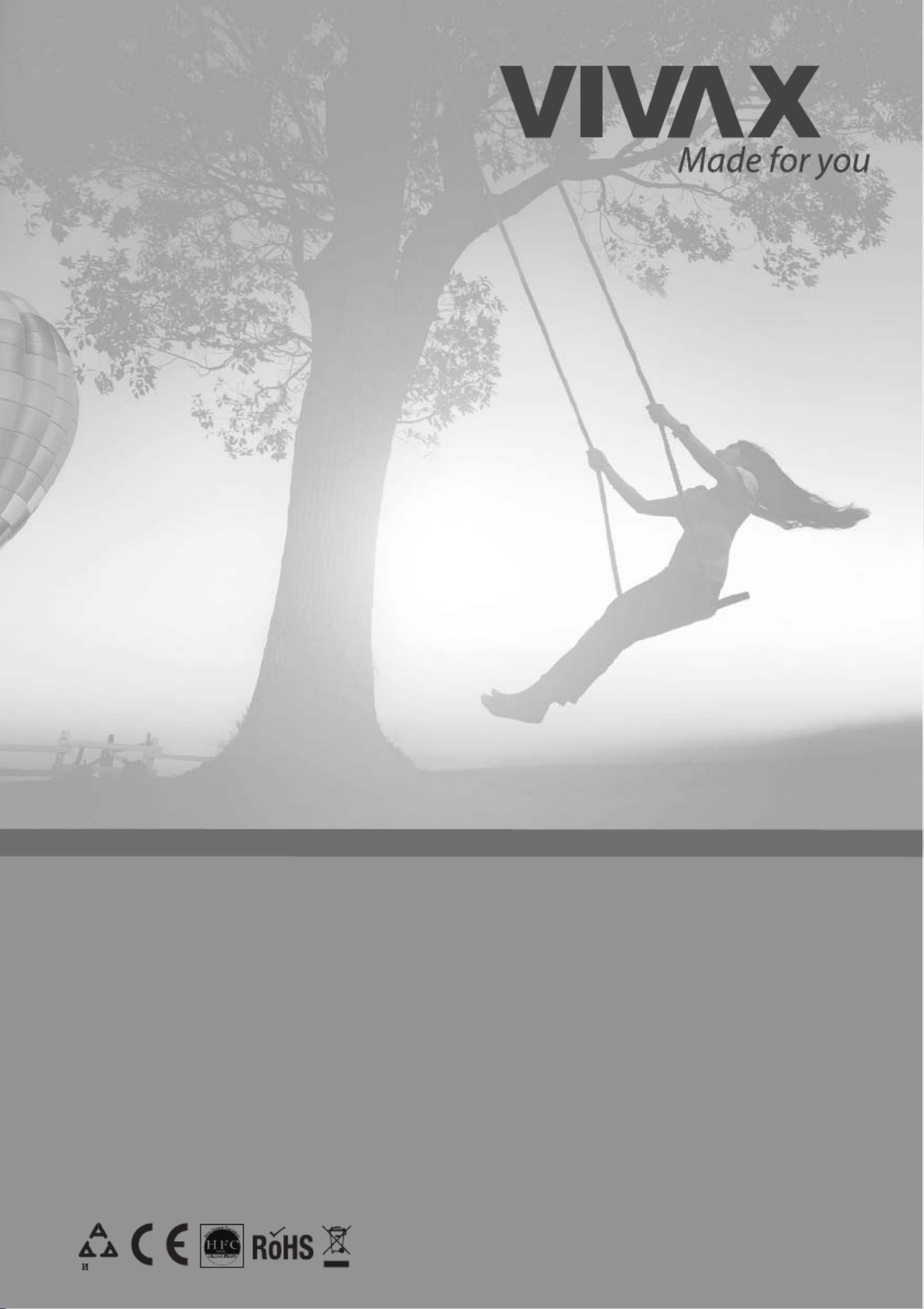
EN
User manual
HPP 24CH70AERI R32-1-
HPP-30CH90AERI R32-1
HPP-41CH120AERI R32-1
035 23
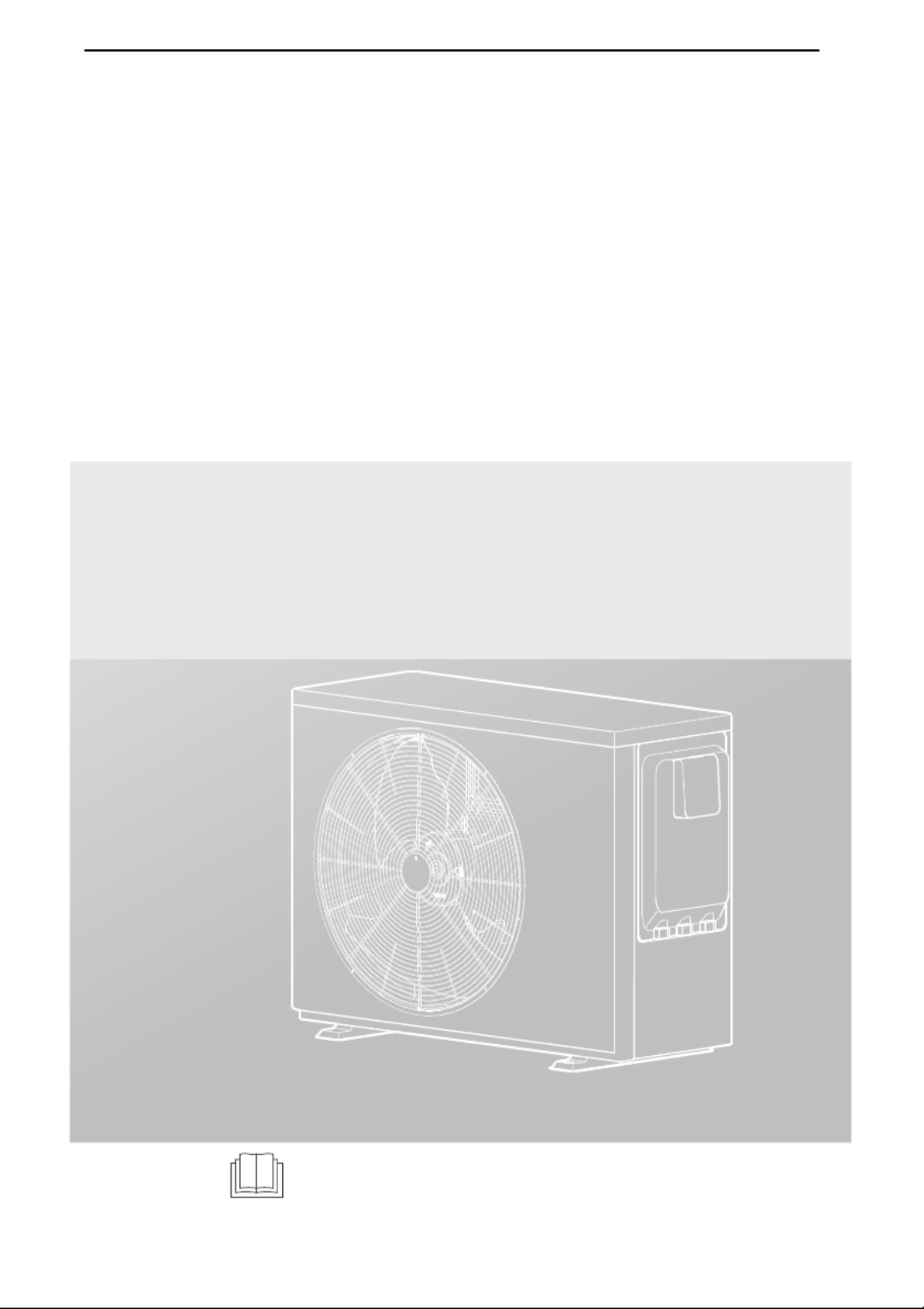
Swimming pool heat pump
INSTALLATION
AND OWNER’S MANUAL
Thank you very much for purchasing our product.
Before using your unit, please read this manual carefully and keep it for future reference.
IMPORTANT NOTE:
ENG VIVAX
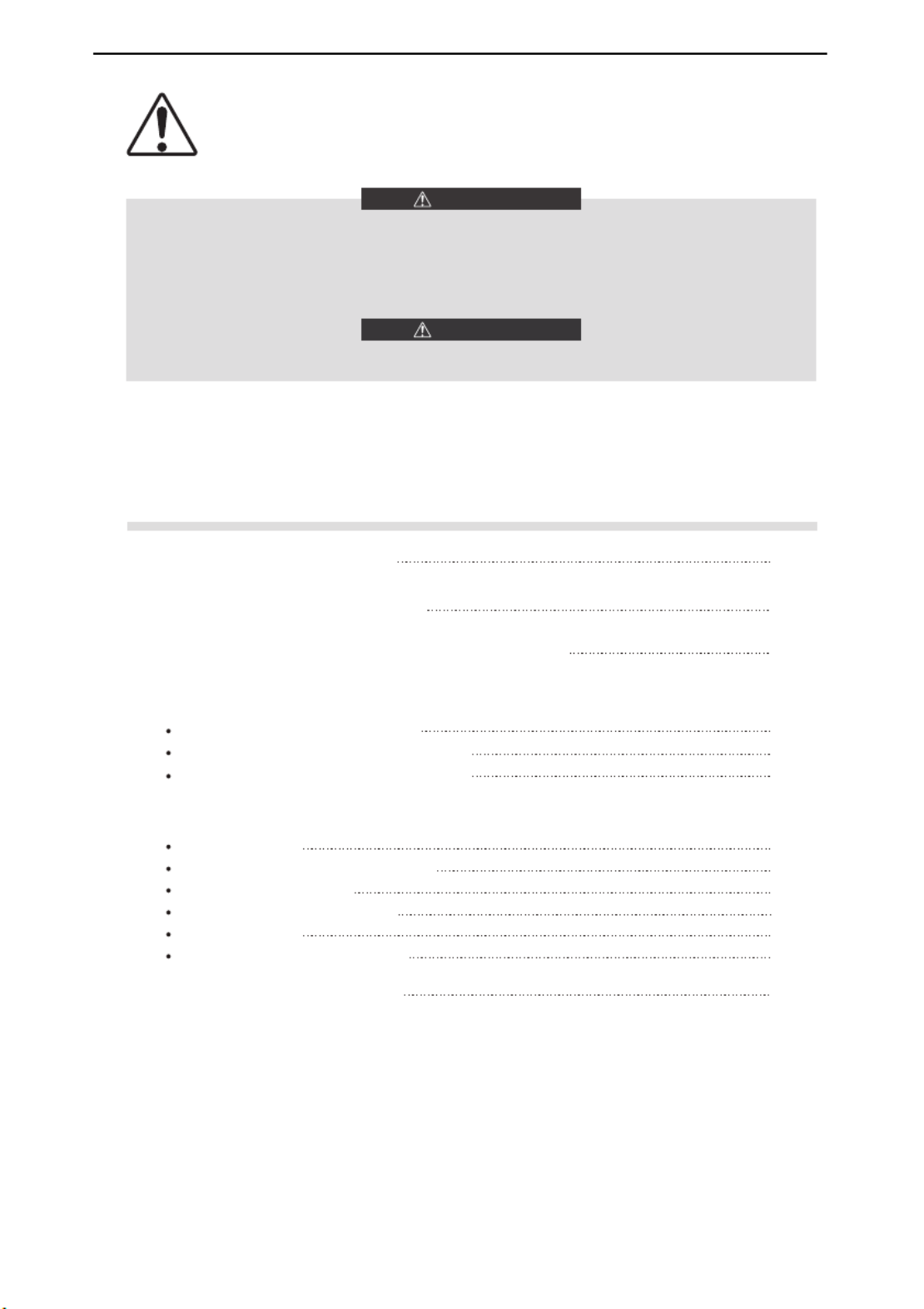
CONTENTS
05
05
3
2
07
06
4
5
08
10
08
12
6
Dimensions
Shock Absorption and Fixations
Drain Hole Position
Inlet & Outlet Water Pipes
Field Wiring
Safety Device Requirement
Location Space Requirement
Location Selection In Cold Climates
Location Selection In Direct Sunlight
4.1
4.2
4.3
11
10
09
5.1
5.2
5.3
5.4
5.5
5.6
02
1
SAFETY PRECAUTIONS
ACCESSORIES SUPPLIED WITH THE UNIT
GENERAL INTRODUCTION
INSTALLATION SITE
INSTALLATION PRECAUTIONS
TYPICAL APPLICATIONS
07
RECOGNIZE THIS SYMBOL AS AN INDICATION OF IMPORTANT
SAFETY INFORMATION
WARNING
These instructions are intended as an aid to qualified licensed service personnel for proper installation, adjustment
and operation of this unit. Read these instructions thoroughly before attempting installation or operation. Failure to
follow these instructions may result in improper installation, adjustment, service or maintenance possibly resulting in
fire, electrical shock, property damage, personal injury or death.
CAUTION
Please drain water when the unit is not in use in winter to avoid freeze damage.
VIVAX ENG
Produktspezifikationen
Marke: | Vivax |
Kategorie: | Wärmepumpe |
Modell: | HPP-24CH70AERI R32-1 |
Brauchst du Hilfe?
Wenn Sie Hilfe mit Vivax HPP-24CH70AERI R32-1 benötigen, stellen Sie unten eine Frage und andere Benutzer werden Ihnen antworten
Bedienungsanleitung Wärmepumpe Vivax

31 August 2024

29 August 2024

28 August 2024

28 August 2024

28 August 2024

3 Januar 2024
Bedienungsanleitung Wärmepumpe
- Wärmepumpe Samsung
- Wärmepumpe LG
- Wärmepumpe Bosch
- Wärmepumpe AEG
- Wärmepumpe Siemens
- Wärmepumpe ATAG
- Wärmepumpe Electrolux
- Wärmepumpe Miele
- Wärmepumpe Blaupunkt
- Wärmepumpe Grundig
- Wärmepumpe Hotpoint
- Wärmepumpe Inventum
- Wärmepumpe Wilfa
- Wärmepumpe Atlantic
- Wärmepumpe Balay
- Wärmepumpe Mitsubishi
- Wärmepumpe Hisense
- Wärmepumpe Arçelik
- Wärmepumpe Vaillant
- Wärmepumpe Qlima
- Wärmepumpe Junkers
- Wärmepumpe De Dietrich
- Wärmepumpe Remeha
- Wärmepumpe Stiebel Eltron
- Wärmepumpe Viessmann
- Wärmepumpe Orima
- Wärmepumpe Dimplex
- Wärmepumpe Fujitsu
- Wärmepumpe Westinghouse
- Wärmepumpe Baxi
- Wärmepumpe Tesy
- Wärmepumpe Itho Daalderop
- Wärmepumpe Carrier
- Wärmepumpe Gree
- Wärmepumpe Olimpia Splendid
- Wärmepumpe Danfoss
- Wärmepumpe Ferroli
- Wärmepumpe Nibe
- Wärmepumpe Daikin
- Wärmepumpe Fisher & Paykel
- Wärmepumpe Elco
- Wärmepumpe Fairland
- Wärmepumpe Flojet
- Wärmepumpe Harmopool
- Wärmepumpe Hydro-Pro
- Wärmepumpe Maxicool
- Wärmepumpe Nefit
- Wärmepumpe Techneco
- Wärmepumpe Thermor
- Wärmepumpe Wita
- Wärmepumpe Zodiac
- Wärmepumpe AstralPool
- Wärmepumpe JANDY
- Wärmepumpe Armstrong
- Wärmepumpe MRCOOL
- Wärmepumpe Wilo
- Wärmepumpe Grundfos
- Wärmepumpe Kospel
- Wärmepumpe Waterco
- Wärmepumpe Alpha Innotec
- Wärmepumpe AWB
- Wärmepumpe Azuro
- Wärmepumpe Calorex
Neueste Bedienungsanleitung für -Kategorien-

3 Dezember 2024
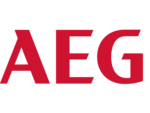
1 Oktober 2024
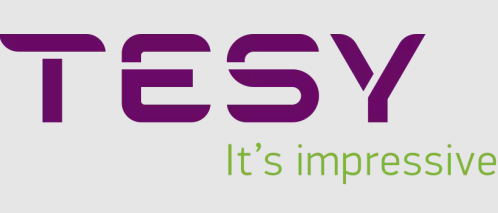
30 September 2024

21 September 2024

19 September 2024

16 September 2024

13 September 2024

7 September 2024

7 September 2024

7 September 2024