Fujitsu AOEG18KBCA2 Bedienungsanleitung
Fujitsu
Klimaanlage
AOEG18KBCA2
Lesen Sie kostenlos die 📖 deutsche Bedienungsanleitung für Fujitsu AOEG18KBCA2 (13 Seiten) in der Kategorie Klimaanlage. Dieser Bedienungsanleitung war für 21 Personen hilfreich und wurde von 2 Benutzern mit durchschnittlich 4.5 Sternen bewertet
Seite 1/13
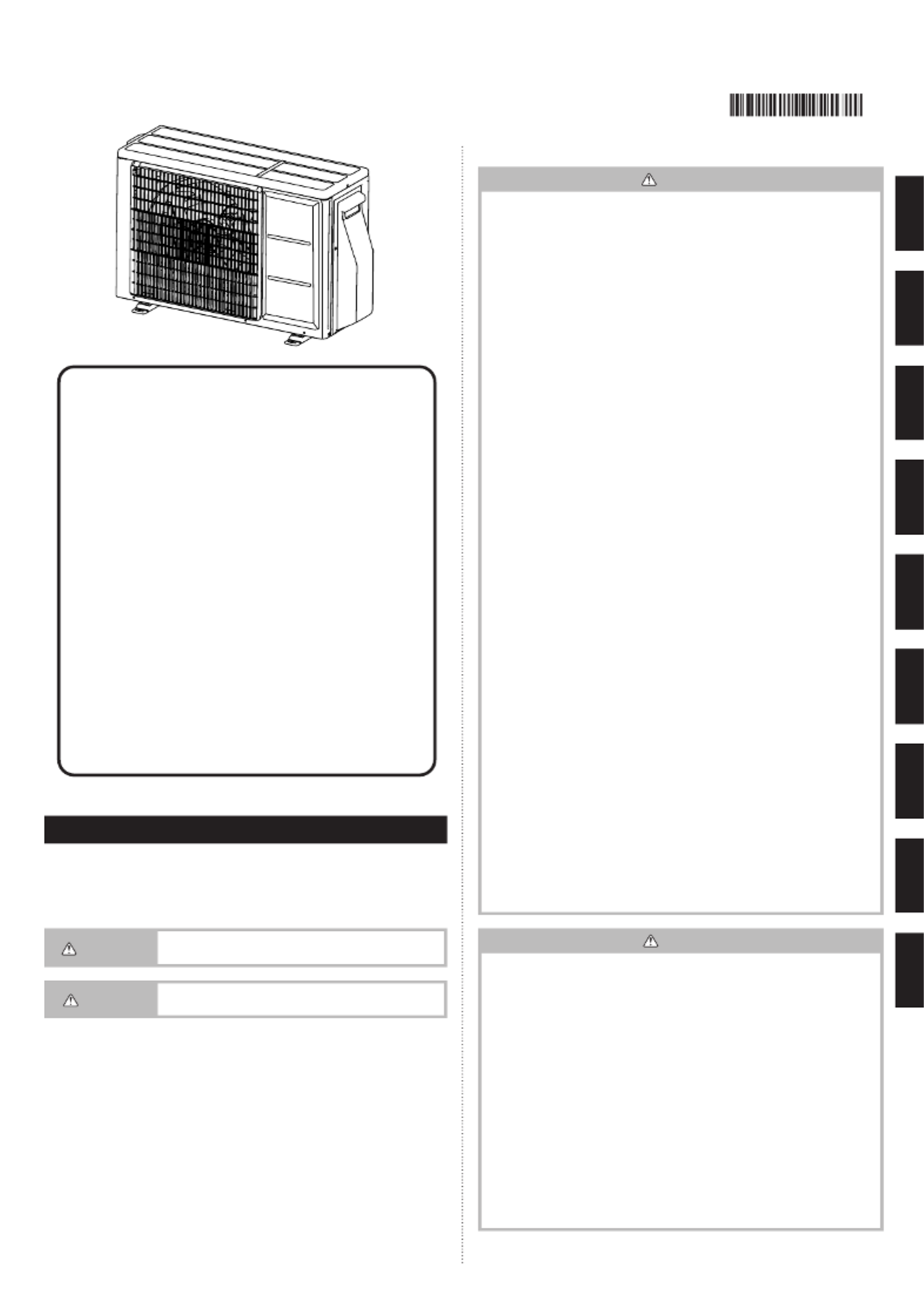
En-1
WARNING
• Installation of this product must be done by experienced service technicians or
professional installers only in accordance with this manual. Installation by nonprofes-
sional or improper installation of the product may cause serious accidents such as
injury, water leakage, electric shock, or fi re. If the product is installed in disregard of
the instructions in this manual, it will void the manufacturer’s warranty.
• To avoid getting an electric shock, never touch the electrical components soon
after the power supply has been turned off . After turning off the power, always wait
10 minutes or more before you touch the electrical components.
• Do not turn on the power until all work has been completed. Turning on the power
before the work is completed can cause serious accidents such as electric shock or
fi re.
• If refrigerant leaks while work is being carried out, ventilate the area. If the refrigerant
comes in contact with a fl ame, it produces a toxic gas.
• Installation must be performed in accordance with regulations, codes, or standards
for electrical wiring and equipment in each country, region, or the installation place.
• Do not use this equipment with air or any other unspecifi ed refrigerant in the refriger-
ant lines. Excess pressure can cause a rupture.
• During installation, make sure that the refrigerant pipe is attached fi rmly before you
run the compressor.
Do not operate the compressor under the condition of refrigerant piping not attached
properly with 3-way valve open. This may cause abnormal pressure in the refrigera-
tion cycle that leads to rupture and even injury.
• When installing or relocating the air conditioner, do not mix gases other than the
specifi ed refrigerant (R32) to enter the refrigerant cycle.
If air or other gas enters the refrigerant cycle, the pressure inside the cycle will rise to
an abnormally high value and cause rupture, injury, etc.
• To connect the indoor unit and outdoor unit, use air conditioner piping and cables
available locally as standard parts. This manual describes proper connections using
such installation set.
• Do not modify power cable, use extension cable or branch wiring. Improper use may
cause electric shock or fi re by poor connection, insuffi cient insulation or over current.
• Do not purge the air with refrigerants but use a vacuum pump to vacuum the installa-
tion.
• There is not extra refrigerant in the outdoor unit for air purging.
• Use a vacuum pump for R32 or R410A exclusively.
• Using the same vacuum pump for diff erent refrigerants may damage the vacuum
pump or the unit.
• Use a clean gauge manifold and charging hose for R32 or R410A exclusively.
• Do not use means to accelerate the defrosting process or to clean, other than those
recommended by the manufacturer.
• The appliance shall be stored in a room without continuously operating ignition
sources (for example: open fl ames, an operating gas appliance or an operating
electric heater).
• Do not pierce or burn.
• Be aware that refrigerants may not contain an odour.
• During the pump-down operation, make sure that the compressor is turned off before
you remove the refrigerant piping.
Do not remove the connection pipe while the compressor is in operation with 3-way
valve open.
This may cause abnormal pressure in the refrigeration cycle that leads to rupture and
even injury.
• This appliance is not intended for use by persons (including children) with reduced
physical, sensory or mental capabilities, or lack of experience and knowledge, unless
they have been given supervision or instruction concerning use of the appliance by a
person responsible for their safety. Children should be supervised to ensure that they
do not play with the appliance.
CAUTION
• For the air conditioner to work appropriately, install it as written in this manual.
• The appliance shall not be installed in an unventilated space, if that space is smaller
than 1.61 m2.
• This product must be installed by qualifi ed personnel with a capacity certifi cation of
handling refrigerant fl uids. Refer to regulation and laws in use on installation place.
• Install the product by following local codes and regulations in force at the place of
installation, and the instructions provided by the manufacturer.
• This product is part of a set constituting an air conditioner. The product must not be
installed alone or be installed with non-authorized device by the manufacturer.
• Always use a separate power supply line protected by a circuit breaker operating on
all wires with a distance between contact of 3 mm for this product.
• To protect the persons, earth (ground) the product correctly, and use the power cable
combined with an Earth Leakage Circuit Breaker (ELCB).
• This product is not explosion proof, and therefore should not be installed in explosive
atmosphere.
• This product contains no user-serviceable parts. Always consult experienced service
technicians for repairing.
• When moving or relocating the air conditioner, consult experienced service techni-
cians for disconnection and reinstallation of the product.
• Do not touch the fi ns of the heat exchanger. Touching the heat exchanger fi ns could
result in damage to the fi ns or personal injury such as skin rupture.
AIR CONDITIONER
OUTDOOR UNIT
INSTALLATION MANUAL
PART No. 9319205908-01
1. SAFETY PRECAUTIONS
• Be sure to read this manual thoroughly before installation.
• The warnings and precautions indicated in this manual contain important information
pertaining to your safety. Be sure to observe them.
• Hand this manual, together with the operating manual, to the customer. Request the
customer to keep them on hand for future use, such as for relocating or repairing the
unit.
WARNING
Indicates a potentially or imminently hazardous situation
which, if not avoided, could result in death or serious injury.
CAUTION
Indicates a potentially hazardous situation that may result in
minor or moderate injury or damage to property.
[Original instructions] For authorized service personnel only.
EnglishDeutschFrançaisEspañolItalianoE vIkλλη άPortuguêsРусский
Türkçe
Türkçe
Contents
1. SAFETY PRECAUTIONS ....................................................................... 1
2. PRODUCT SPECIFICATION ................................................................. 3
2.1. Installation tools ........................................................................... 3
2.2. Accessories ................................................................................. 4
2.3. Pipe requirements ....................................................................... 4
2.4. Electrical requirements ................................................................ 5
2.5. Additional charge amount ............................................................ 6
2.6. General information ..................................................................... 6
3. INSTALLATION WORK ..........................................................................6
3.1. Installation dimensions ................................................................ 6
3.2. Mounting the unit ......................................................................... 7
3.3. Removing and replacing part .......................................................8
3.4. Drain installation ..........................................................................8
3.5. Pipe installation ...........................................................................8
3.6. Sealing test .................................................................................. 9
3.7. Vacuum process .......................................................................... 9
3.8. Additional charging .................................................................... 10
3.9. Electrical wiring .......................................................................... 10
4. TEST RUN ............................................................................................ 12
4.1. Make a TEST RUN in accordance with the installation
Manual for the indoor unit .......................................................... 12
5. FINISHING ........................................................................................... 12
5.1. Installing insulation .................................................................... 12
6. PUMP DOWN ....................................................................................... 12
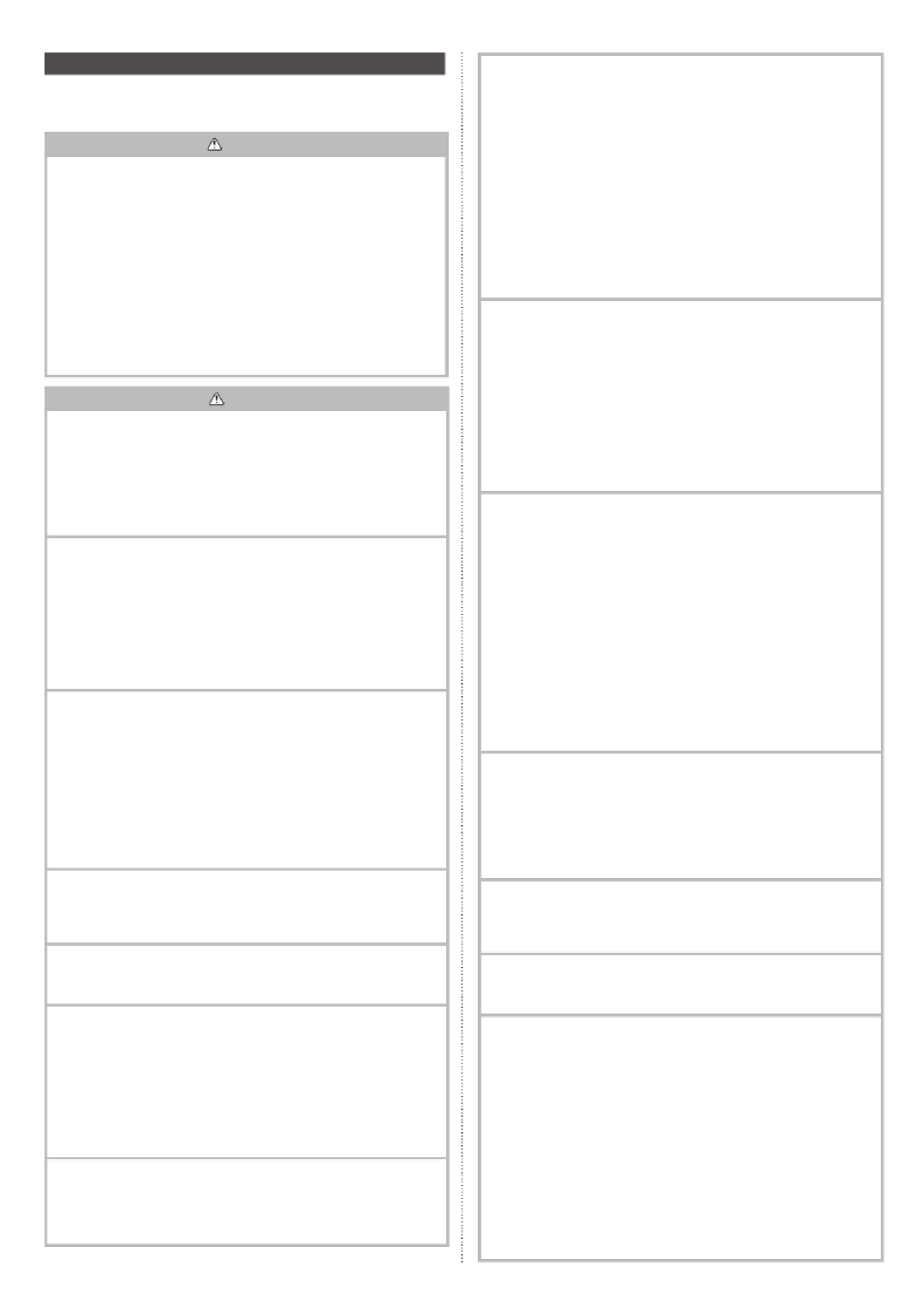
En-2
2-7. Checks to the refrigeration equipment
• Where electrical components are being changed, they shall be fi t for the purpose
and to the correct specifi cation.
• At all times the manufacturer’s maintenance and service guidelines shall be followed.
• If in doubt consult the manufacturer’s technical department for assistance.
• The following checks shall be applied to installations using fl ammable refrigerants.
- The charge size is in accordance with the room size within which the refrigerant
containing parts are installed.
- The ventilation machinery and outlets are operating adequately and are not
obstructed.
- If an indirect refrigerating circuit is being used, the secondary circuit shall be
checked for the presence of refrigerant.
- Marking to the equipment continues to be visible and legible. Markings and signs
that are illegible shall be corrected.
- Refrigeration pipe or components are installed in a position where they are unlikely
to be exposed to any substance which may corrode refrigerant containing compo-
nents, unless the components are constructed of materials which are inherently
resistant to being corroded or are suitably protected against being so corroded.
2-8. Checks to electrical devices
• Repair and maintenance to electrical components shall include initial safety checks
and component inspection procedures.
• If a fault exists that could compromise safety, then no electrical supply shall be
connected to the circuit until it is satisfactorily dealt with.
• If the fault cannot be corrected immediately but it is necessary to continue opera-
tion, an adequate temporary solution shall be used.
• This shall be reported to the owner of the equipment so all parties are advised.
• Initial safety checks shall include.
- That capacitors are discharged: this shall be done in a safe manner to avoid
possibility of sparking.
- That there no live electrical components and wiring are exposed while charging,
recovering or purging the system.
- That there is continuity of earth bonding.
3. Repairs to sealed components
• During repairs to sealed components, all electrical supplies shall be disconnected
from the equipment being worked upon prior to any removal of sealed covers, etc.
• If it is absolutely necessary to have an electrical supply to equipment during servic-
ing, then a permanently operating form of leak detection shall be located at the
most critical point to warn of a potentially hazardous situation.
• Particular attention shall be paid to the following to ensure that by working on
electrical components, the casing is not altered in such a way that the level of
protection is aff ected.
• This shall include damage to cables, excessive number of connections, terminals
not made to original specifi cation, damage to seals, incorrect fi tting of glands, etc.
• Ensure that apparatus is mounted securely.
• Ensure that seals or sealing materials have not degraded such that they no longer
serve the purpose of preventing the ingress of fl ammable atmospheres.
• Replacement parts shall be in accordance with the manufacturer’s specifi cations.
NOTE: The use of silicon sealant may inhibit the eff ectiveness of some types of leak
detection equipment.
Intrinsically safe components do not have to be isolated prior to working on
them.
4. Repair to intrinsically safe components
• Do not apply any permanent inductive or capacitance loads to the circuit without
ensuring that this will not exceed the permissible voltage and current permitted for
the equipment in use.
• Intrinsically safe components are the only types that can be worked on while live in
the presence of a fl ammable atmosphere.
• The test apparatus shall be at the correct rating.
• Replace components only with parts specifi ed by the manufacturer.
• Other parts may result in the ignition of refrigerant in the atmosphere from a leak.
5. Cabling
• Check that cabling will not be subject to wear, corrosion, excessive pressure, vibra-
tion, sharp edges or any other adverse environmental eff ects.
• The check shall also take into account the eff ects of aging or continual vibration
from sources such as compressors or fans.
6. Detection of fl ammable refrigerants
• Under no circumstances shall potential sources of ignition be used in the searching
for or detection of refrigerant leaks.
• A halide torch (or any other detector using a naked fl ame) shall not be used.
7. Leak detection methods
• Electronic leak detectors shall be used to detect fl ammable refrigerants, but the
sensitivity may not be adequate, or may need re-calibration. (Detection equipment
shall be calibrated in a refrigerant-free area.)
• Ensure that the detector is not a potential source of ignition and is suitable for the
refrigerant used.
• Leak detection equipment shall be set at a percentage of the LFL of the refrigerant
and shall be calibrated to the refrigerant employed and the appropriate percentage
of gas (25 % maximum) is confi rmed.
• Leak detection fl uids are suitable for use with most refrigerants but the use of
detergents containing chlorine shall be avoided as the chlorine may react with the
refrigerant and corrode the copper pipe-work.
• If a leak is suspected, all naked fl ames shall be removed/extinguished.
• If a leakage of refrigerant is found which requires brazing, all of the refrigerant shall
be recovered from the system, or isolated (by means of shut off valves) in a part of
the system remote from the leak.
Oxygen free nitrogen (OFN) shall then be purged through the system both before
and during the brazing process.
Precautions for using R32 refrigerant
The basic installation work procedures are the same as conventional refrigerant (R410A,
R22) models.
However, pay careful attention to the following points:
WARNING
• Since the working pressure is 1.6 times higher than that of refrigerant R22 models,
some of the piping and installation and service tools are special. (See “2.1. Installation
tools”
.)
Especially, when replacing a refrigerant R22 model with a new refrigerant R32 model,
always replace the conventional piping and fl are nuts with the R32 and R410A piping
and fl are nuts on the outdoor unit side.
For R32 and R410A, the same fl are nut on the outdoor unit side and pipe can be
used.
• Models that use refrigerant R32 and R410A have a diff erent charging port thread
diameter to prevent erroneous charging with refrigerant R22 and for safety. There-
fore, check beforehand. [The charging port thread diameter for R32 and R410A is 1/2
inch.]
• Be more careful than R22 so that foreign matter (oil, water, etc.) does not enter the
piping.
Also, when storing the piping, securely seal the opening by pinching, taping, etc.
(Handling of R32 is similar to R410A.)
CAUTION
1. Installation (Space)
• That the installation of pipe-work shall be kept to a minimum.
• That pipe-work shall be protected from physical damage.
• That compliance with national gas regulations shall be observed.
• That mechanical connections shall be accessible for maintenance purposes.
• In cases that require mechanical ventilation, ventilation openings shall be kept
clear of obstruction.
• When disposing of the product is used, be based on national regulations, properly
processed.
2. Servicing
2-1. Service personnel
• Any person who is involved with working on or breaking into a refrigerant circuit
should hold a current valid certifi cate from an industry-accredited assessment
authority, which authorizes their competence to handle refrigerants safely in ac-
cordance with an industry recognised assessment specifi cation.
• Servicing shall only be performed as recommended by the equipment manufac-
turer. Maintenance and repair requiring the assistance of other skilled personnel
shall be carried out under the supervision of the person competent in the use of
fl ammable refrigerants.
• Servicing shall be performed only as recommended by the manufacturer.
2-2. Work
• Prior to beginning work on systems containing fl ammable refrigerants, safety
checks are necessary to ensure that the risk of ignition is minimised. For repair to
the refrigerating system, the precautions in 2-2 to 2-8 shall be complied with prior
to conducting work on the system.
• Work shall be undertaken under a controlled procedure so as to minimize the risk
of a fl ammable gas or vapour being present while the work is being performed.
• All maintenance staff and others working in the local area shall be instructed on the
nature of work being carried out.
• Work in confi ned spaces shall be avoided.
• The area around the workspace shall be sectioned off .
• Ensure that the conditions within the area have been made safe by control of fl am-
mable material.
2-3. Checking for presence of refrigerant
• The area shall be checked with an appropriate refrigerant detector prior to and dur-
ing work, to ensure the technician is aware of potentially fl ammable atmospheres.
• Ensure that the leak detection equipment being used is suitable for use with fl am-
mable refrigerants, i.e. non sparking, adequately sealed or intrinsically safe.
2-4. Presence of fi re extinguisher
• If any hot work is to be conducted on the refrigeration equipment or any associated
parts, appropriate fi re extinguishing equipment shall be available at hand.
• Have a dry powder or CO2 fi re extinguisher adjacent to the charging area.
2-5. No ignition sources
• No person carrying out work in relation to a refrigeration system which involves
exposing any pipe work that contains or has contained fl ammable refrigerant shall
use any sources of ignition in such a manner that it may lead to the risk of fi re or
explosion.
• All possible ignition sources, including cigarette smoking, should be kept suffi cient-
ly far away from the site of installation, repairing, removing and disposal, during
which fl ammable refrigerant can possibly be released to the surrounding space.
• Prior to work taking place, the area around the equipment is to be surveyed to
make sure that there are no fl ammable hazards or ignition risks. “No Smoking”
signs shall be displayed.
2-6. Ventilated area
• Ensure that the area is in the open or that it is adequately ventilated before break-
ing into the system or conducting any hot work.
• A degree of ventilation shall continue during the period that the work is carried out.
• The ventilation should safely disperse any released refrigerant and preferably
expel it externally into the atmosphere.
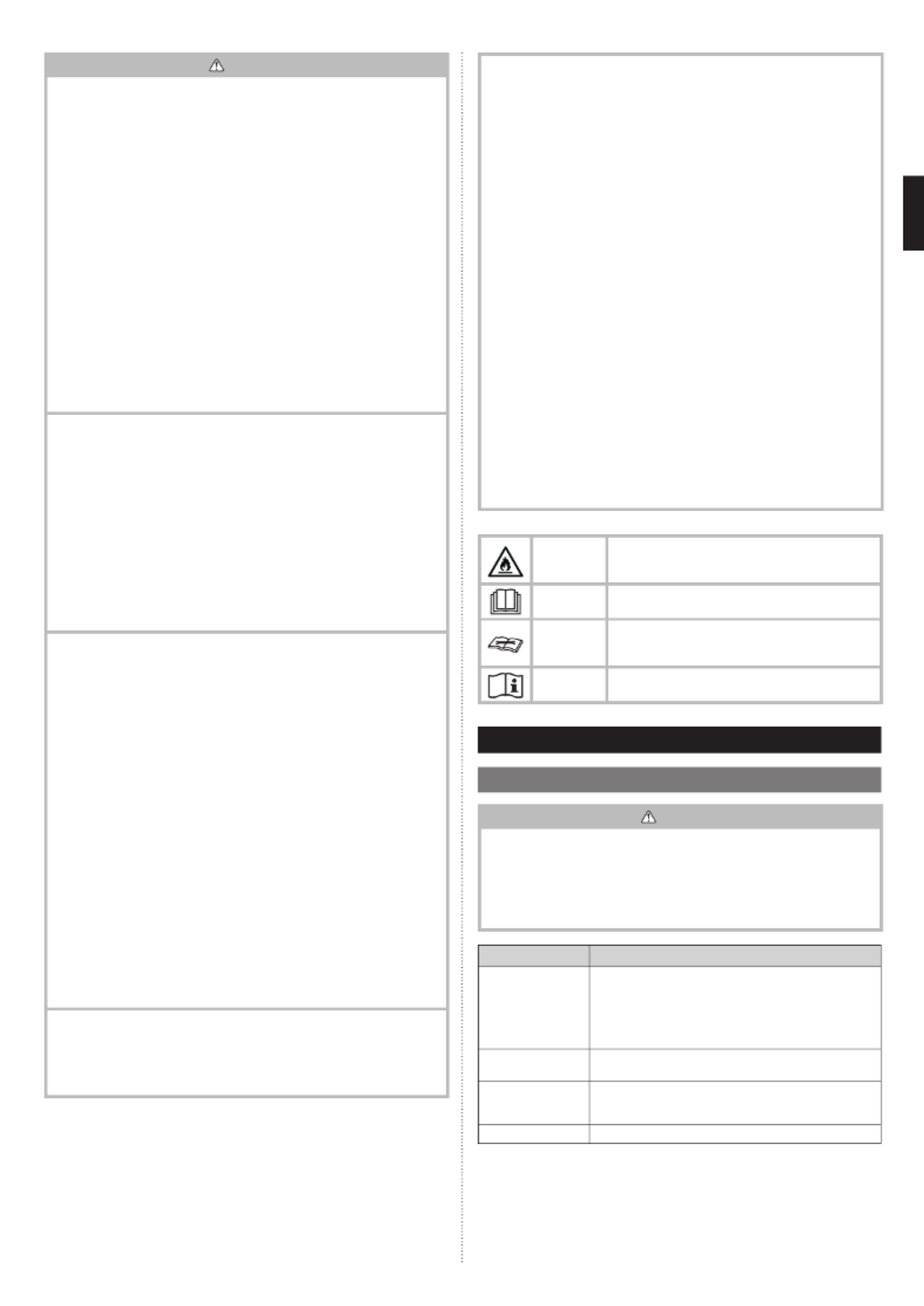
En-3
CAUTION
8. Removal and evacuation
• When breaking into the refrigerant circuit to make repairs – or for any other
purpose –conventional procedures shall be used.
However, it is important that best practice is followed since fl ammability is a
consideration.
The following procedure shall be adhered to:
• remove refrigerant
• purge the circuit with inert gas
• evacuate
• purge again with inert gas
• open the circuit by cutting or brazing
• The refrigerant charge shall be recovered into the correct recovery cylinders.
• The system shall be “fl ushed” with OFN to render the unit safe.
• This process may need to be repeated several times.
• Compressed air or oxygen shall not be used for this task.
• Flushing shall be achieved by breaking the vacuum in the system with OFN and
continuing to fi ll until the working pressure is achieved, then venting to atmosphere,
and fi nally pulling down to a vacuum.
• This process shall be repeated until no refrigerant is within the system.
• When the fi nal OFN charge is used, the system shall be vented down to atmo-
spheric pressure to enable work to take place.
• This operation is absolutely vital if brazing operations on the pipe work are to take
place.
• Ensure that the outlet for the vacuum pump is not close to any ignition sources and
there is ventilation available.
9. Charging procedures
• In addition to conventional charging procedures, the following requirements shall
be followed.
- Ensure that contamination of diff erent refrigerants does not occur when using
charging equipment.
- Hoses or lines shall be as short as possible to minimize the amount of refriger-
ant contained in them.
- Cylinders shall be kept upright.
- Ensure that the refrigeration system is earthed prior to charging the system with
refrigerant.
- Label the system when charging is complete (if not already).
- Extreme care shall be taken not to overfi ll the refrigeration system.
• Prior to recharging the system it shall be pressure tested with OFN.
• The system shall be leak tested on completion of charging but prior to commis-
sioning.
• A follow up leak test shall be carried out prior to leaving the site.
10. Decommissioning
• Before carrying out this procedure, it is essential that the technician is completely
familiar with the equipment and all its details.
• It is recommended good practice that all refrigerants are recovered safely.
• Prior to the task being carried out, an oil and refrigerant sample shall be taken in
case analysis is required prior to re-use of reclaimed refrigerant.
• It is essential that electrical power is available before the task is commenced.
a) Become familiar with the equipment and its operation.
b) Isolate system electrically.
c) Before attempting the procedure ensure that:
• mechanical handling equipment is available, if required, for handling refrig-
erant cylinders;
• all personal protective equipment is available and being used correctly;
• the recovery process is supervised at all times by a competent person;
• recovery equipment and cylinders conform to the appropriate standards.
d) Pump down refrigerant system, if possible.
e) If a vacuum is not possible, make a manifold so that refrigerant can be re-
moved from various parts of the system.
f) Make sure that cylinder is situated on the scales before recovery takes place.
g) Start the recovery machine and operate in accordance with manufacturer’s
instructions.
h) Do not overfi ll cylinders. (No more than 80 % volume liquid charge).
i) Do not exceed the maximum working pressure of the cylinder, even temporarily.
j) When the cylinders have been fi lled correctly and the process completed, make
sure that the cylinders and the equipment are removed from site promptly and
all isolation valves on the equipment are closed off .
k) Recovered refrigerant shall not be charged into another refrigeration system
unless it has been cleaned and checked.
11. Labelling
• Equipment shall be labelled stating that it has been de-commissioned and emptied
of refrigerant.
• The label shall be dated and signed.
• Ensure that there are labels on the equipment stating the equipment contains fl am-
mable refrigerant.
12. Recovery
• When removing refrigerant from a system, either for servicing or decommissioning,
it is recommended good practice that all refrigerants are removed safely.
• When transferring refrigerant into cylinders, ensure that only appropriate refrigerant
recovery cylinders are employed.
• Ensure that the correct number of cylinders for holding the total system charge are
available.
• All cylinders to be used are designated for the recovered refrigerant and labelled
for that refrigerant (i.e. special cylinders for the recovery of refrigerant).
• Cylinders shall be complete with pressure relief valve and associated shut-off
valves in good working order.
• Empty recovery cylinders are evacuated and, if possible, cooled before recovery
occurs.
• The recovery equipment shall be in good working order with a set of instructions
concerning the equipment that is at hand and shall be suitable for the recovery of
fl ammable refrigerants.
• In addition, a set of calibrated weighing scales shall be available and in good work-
ing order.
• Hoses shall be complete with leak-free disconnect couplings and in good condition.
• Before using the recovery machine, check that it is in satisfactory working order,
has been properly maintained and that any associated electrical components are
sealed to prevent ignition in the event of a refrigerant release.
Consult manufacturer if in doubt.
• The recovered refrigerant shall be returned to the refrigerant supplier in the correct
recovery cylinder, and the relevant Waste Transfer Note arranged.
• Do not mix refrigerants in recovery units and especially not in cylinders.
• If compressors or compressor oils are to be removed, ensure that they have been
evacuated to an acceptable level to make certain that fl ammable refrigerant does
not remain within the lubricant.
• The evacuation process shall be carried out prior to returning the compressor to
the suppliers.
• Only electric heating to the compressor body shall be employed to accelerate this
process.
• When oil is drained from a system, it shall be carried out safely.
Explanation of symbols displayed on the indoor unit or outdoor unit.
WARNING
This symbol shows that this equipment uses a fl ammable
refrigerant. If the refrigerant is leaked, together with an
external ignition source, there is a possibility of ignition.
CAUTION This symbol shows that the Operation Manual should be
read carefully.
CAUTION
This symbol shows that a service personnel should be
handling this equipment with reference to the Installation
Manual.
CAUTION This symbol shows that there is information included in the
Operation Manual and/or Installation Manual.
2. PRODUCT SPECIFICATION
2.1. Installation tools
WARNING
• To install a unit that uses R32 refrigerant, use dedicated tools and piping materials that
have been manufactured specifi cally for R32(R410A) use. Because the pressure of
R32 refrigerant is approximately 1.6 times higher than R22, failure to use dedicated
piping material or improper installation can cause rupture or injury. Furthermore, it can
cause serious accidents such as water leakage, electric shock, or fi re.
• Do not use a vacuum pump or refrigerant recovery tools with a series motor, since it
may ignite.
Tool name Contents of change
Gauge manifold Pressure is high and cannot be measured with a conventional
(R22) gauge. To prevent erroneous mixing of other refriger-
ants, the diameter of each port has been changed.
It is recommended the gauge with seals -0.1 to 5.3 MPa
(-1 to 53 bar) for high pressure. -0.1 to 3.8 MPa (-1 to 38 bar)
for low pressure.
Charge hose To increase pressure resistance, the hose material and base
size were changed. (R32/R410A)
Vacuum pump A conventional vacuum pump can be used by installing a
vacuum pump adapter.
(Use of a vacuum pump with a series motor is prohibited.)
Gas leakage detector Special gas leakage detector for HFC refrigerant R32/R410A.
■ Copper pipes
It is necessary to use seamless copper pipes and it is desirable that the amount of residual
oil is less than 40 mg/10 m. Do not use copper pipes having a collapsed, deformed or
discolored portion (especially on the interior surface). Otherwise, the expansion valve or
capillary tube may become blocked with contaminants.
As an air conditioner using R32(R410A) incurs pressure higher than when using conven-
tional refrigerant, it is necessary to choose adequate materials.
Produktspezifikationen
Marke: | Fujitsu |
Kategorie: | Klimaanlage |
Modell: | AOEG18KBCA2 |
Brauchst du Hilfe?
Wenn Sie Hilfe mit Fujitsu AOEG18KBCA2 benötigen, stellen Sie unten eine Frage und andere Benutzer werden Ihnen antworten
Bedienungsanleitung Klimaanlage Fujitsu

9 Oktober 2024

9 Oktober 2024

9 Oktober 2024

8 Oktober 2024

7 Oktober 2024

4 Oktober 2024

3 Oktober 2024

2 Oktober 2024

29 September 2024

26 September 2024
Bedienungsanleitung Klimaanlage
- Klimaanlage Samsung
- Klimaanlage Infiniton
- Klimaanlage Clatronic
- Klimaanlage Domo
- Klimaanlage Emerio
- Klimaanlage G3 Ferrari
- Klimaanlage Tristar
- Klimaanlage Sanyo
- Klimaanlage Manta
- Klimaanlage Medion
- Klimaanlage Nedis
- Klimaanlage Panasonic
- Klimaanlage Profile
- Klimaanlage LG
- Klimaanlage Adler
- Klimaanlage Bestron
- Klimaanlage Camry
- Klimaanlage Guzzanti
- Klimaanlage Princess
- Klimaanlage Trisa
- Klimaanlage Bosch
- Klimaanlage AEG
- Klimaanlage Ardes
- Klimaanlage Siemens
- Klimaanlage Bauknecht
- Klimaanlage Concept
- Klimaanlage Electrolux
- Klimaanlage Gorenje
- Klimaanlage Klarstein
- Klimaanlage Koenic
- Klimaanlage Teesa
- Klimaanlage Unold
- Klimaanlage Whirlpool
- Klimaanlage Alaska
- Klimaanlage Bomann
- Klimaanlage Essentiel B
- Klimaanlage H.Koenig
- Klimaanlage Korona
- Klimaanlage Listo
- Klimaanlage Melissa
- Klimaanlage Russell Hobbs
- Klimaanlage Taurus
- Klimaanlage Vox
- Klimaanlage TechniSat
- Klimaanlage Conrad
- Klimaanlage Day
- Klimaanlage ECG
- Klimaanlage Mesko
- Klimaanlage Telefunken
- Klimaanlage Thomson
- Klimaanlage Black And Decker
- Klimaanlage Trotec
- Klimaanlage Mestic
- Klimaanlage BEKO
- Klimaanlage Blaupunkt
- Klimaanlage Eldom
- Klimaanlage Grundig
- Klimaanlage Heinner
- Klimaanlage Home Electric
- Klimaanlage Hotpoint
- Klimaanlage Inventum
- Klimaanlage Koenig
- Klimaanlage Prime3
- Klimaanlage Primo
- Klimaanlage Sharp
- Klimaanlage Wilfa
- Klimaanlage Dometic
- Klimaanlage Ansonic
- Klimaanlage Ariston
- Klimaanlage Aspes
- Klimaanlage Brandt
- Klimaanlage Candy
- Klimaanlage Comfee
- Klimaanlage Corberó
- Klimaanlage Einhell
- Klimaanlage Daewoo
- Klimaanlage Everglades
- Klimaanlage Exquisit
- Klimaanlage Mitsubishi
- Klimaanlage Finlux
- Klimaanlage GE
- Klimaanlage Haier
- Klimaanlage Hisense
- Klimaanlage Hotpoint-Ariston
- Klimaanlage Bartscher
- Klimaanlage Kelvinator
- Klimaanlage Midea
- Klimaanlage NABO
- Klimaanlage Progress
- Klimaanlage Frigidaire
- Klimaanlage Svan
- Klimaanlage Vestel
- Klimaanlage Zanker
- Klimaanlage Zanussi
- Klimaanlage Philco
- Klimaanlage Eurom
- Klimaanlage Xiaomi
- Klimaanlage Avidsen
- Klimaanlage Akai
- Klimaanlage Arçelik
- Klimaanlage Hitachi
- Klimaanlage Hyundai
- Klimaanlage Orava
- Klimaanlage TCL
- Klimaanlage Toshiba
- Klimaanlage Livoo
- Klimaanlage DCG
- Klimaanlage Kärcher
- Klimaanlage Easy Home
- Klimaanlage Tectro
- Klimaanlage Sencys
- Klimaanlage Bimar
- Klimaanlage Klarbach
- Klimaanlage Lanaform
- Klimaanlage Rowenta
- Klimaanlage Sencor
- Klimaanlage DeLonghi
- Klimaanlage Element
- Klimaanlage Fakir
- Klimaanlage Kalorik
- Klimaanlage OneConcept
- Klimaanlage Rotel
- Klimaanlage Ufesa
- Klimaanlage Tripp Lite
- Klimaanlage Anslut
- Klimaanlage Calor
- Klimaanlage Cecotec
- Klimaanlage Vaillant
- Klimaanlage Termozeta
- Klimaanlage Centurion
- Klimaanlage Climadiff
- Klimaanlage Frilec
- Klimaanlage Inventor
- Klimaanlage Kibernetik
- Klimaanlage Qlima
- Klimaanlage Amcor
- Klimaanlage CHIGO
- Klimaanlage Duux
- Klimaanlage Honeywell
- Klimaanlage Klima1stKlaaS
- Klimaanlage Meaco
- Klimaanlage Remko
- Klimaanlage SHE
- Klimaanlage Sinclair
- Klimaanlage Suntec
- Klimaanlage Wood's
- Klimaanlage Zibro
- Klimaanlage Sigma
- Klimaanlage Globaltronics
- Klimaanlage Moa
- Klimaanlage Carson
- Klimaanlage Livington
- Klimaanlage Airlux
- Klimaanlage Broan
- Klimaanlage Elba
- Klimaanlage MPM
- Klimaanlage Thermex
- Klimaanlage White Knight
- Klimaanlage Logik
- Klimaanlage Team
- Klimaanlage Be Cool
- Klimaanlage Saunier Duval
- Klimaanlage Truma
- Klimaanlage Aermec
- Klimaanlage Orima
- Klimaanlage Proline
- Klimaanlage Dimplex
- Klimaanlage Sonnenkönig
- Klimaanlage Bavaria
- Klimaanlage Heylo
- Klimaanlage Toyotomi
- Klimaanlage Proklima
- Klimaanlage Westinghouse
- Klimaanlage Baxi
- Klimaanlage Amana
- Klimaanlage Carrefour Home
- Klimaanlage Galanz
- Klimaanlage Holland Electro
- Klimaanlage Vivax
- Klimaanlage Profilo
- Klimaanlage Sauber
- Klimaanlage Zelmer
- Klimaanlage Meireles
- Klimaanlage Kogan
- Klimaanlage Royal Sovereign
- Klimaanlage Innoliving
- Klimaanlage Argo
- Klimaanlage HQ
- Klimaanlage Jocca
- Klimaanlage Master
- Klimaanlage Sanus
- Klimaanlage Carrier
- Klimaanlage Edy
- Klimaanlage Frigor
- Klimaanlage Milectric
- Klimaanlage Be Quiet!
- Klimaanlage Insignia
- Klimaanlage Alpatec
- Klimaanlage Artrom
- Klimaanlage Coolix
- Klimaanlage D-Let
- Klimaanlage Gree
- Klimaanlage Gutfels
- Klimaanlage Heiko
- Klimaanlage Olimpia Splendid
- Klimaanlage TOSOT
- Klimaanlage SereneLife
- Klimaanlage Danby
- Klimaanlage APC
- Klimaanlage Ariston Thermo
- Klimaanlage Evolar
- Klimaanlage Ozito
- Klimaanlage Eden
- Klimaanlage Ferroli
- Klimaanlage Blumfeldt
- Klimaanlage RCA
- Klimaanlage Daikin
- Klimaanlage Starlyf
- Klimaanlage Soler & Palau
- Klimaanlage Esatto
- Klimaanlage Orbegozo
- Klimaanlage Dantherm
- Klimaanlage Furrion
- Klimaanlage Oregon Scientific
- Klimaanlage General Electric
- Klimaanlage Ridgid
- Klimaanlage Daitsu
- Klimaanlage Defy
- Klimaanlage Domair
- Klimaanlage Edgestar
- Klimaanlage Emerson
- Klimaanlage Emmeti
- Klimaanlage Fairland
- Klimaanlage Firstline
- Klimaanlage Fral
- Klimaanlage Fronius
- Klimaanlage Fuave
- Klimaanlage Fuji Electric
- Klimaanlage Innova
- Klimaanlage Itho
- Klimaanlage Jocel
- Klimaanlage Just Fire
- Klimaanlage Kenmore
- Klimaanlage Lavorwash
- Klimaanlage Maiko
- Klimaanlage Maxicool
- Klimaanlage MDV
- Klimaanlage Mistral
- Klimaanlage Mizushi
- Klimaanlage Mobile Airco
- Klimaanlage MundoClima
- Klimaanlage Prem-i-air
- Klimaanlage Protector
- Klimaanlage Qlima - Zibro
- Klimaanlage Retro
- Klimaanlage Salton
- Klimaanlage Seally
- Klimaanlage Shinco
- Klimaanlage SMC
- Klimaanlage SMD
- Klimaanlage SPT
- Klimaanlage Stirling
- Klimaanlage Tarrington House
- Klimaanlage Teco
- Klimaanlage Telair
- Klimaanlage Thermo Comfort
- Klimaanlage Trilec
- Klimaanlage Tronix
- Klimaanlage Whynter
- Klimaanlage Zymbo
- Klimaanlage Argoclima
- Klimaanlage Elgin
- Klimaanlage Kunft
- Klimaanlage Becken
- Klimaanlage Rinnai
- Klimaanlage Ravanson
- Klimaanlage Godrej
- Klimaanlage Friedrich
- Klimaanlage NewAir
- Klimaanlage Klimaire
- Klimaanlage EcoFlow
- Klimaanlage Andrews
- Klimaanlage Convair
- Klimaanlage Brivis
- Klimaanlage Malmbergs
- Klimaanlage Challenge
- Klimaanlage Arctic King
- Klimaanlage ElectriQ
- Klimaanlage Luma Comfort
- Klimaanlage Aircooler
- Klimaanlage Acson
- Klimaanlage Volteno
- Klimaanlage Geist
- Klimaanlage Monzana
- Klimaanlage Simplicity
- Klimaanlage Kaden
- Klimaanlage Equation
- Klimaanlage Daizuki
- Klimaanlage Cool Breeze
- Klimaanlage Braemar
- Klimaanlage Equator
- Klimaanlage Khind
- Klimaanlage Krone
- Klimaanlage GoldAir
- Klimaanlage American Comfort
- Klimaanlage Riffel
- Klimaanlage Airwell
- Klimaanlage Bonaire
- Klimaanlage MRCOOL
- Klimaanlage Arcoaire
- Klimaanlage Companion
- Klimaanlage SEEGER
- Klimaanlage Heat Controller
- Klimaanlage LERAN
- Klimaanlage IFB
- Klimaanlage ActronAir
- Klimaanlage Consul
- Klimaanlage HTW
- Klimaanlage B-Air
- Klimaanlage Schabus
- Klimaanlage Mabe
- Klimaanlage House & Luft
- Klimaanlage DEXP
- Klimaanlage Evapcool
- Klimaanlage Aerian
- Klimaanlage Ocean Breeze
- Klimaanlage Commercial Cool
- Klimaanlage Kaco
- Klimaanlage InAlto
- Klimaanlage Climachill
- Klimaanlage Create
- Klimaanlage Bodin
- Klimaanlage ARCTIC WIND
- Klimaanlage JHS
- Klimaanlage Keystone
- Klimaanlage FREONIC
- Klimaanlage Big Ass Fans
- Klimaanlage Electroline
- Klimaanlage Omega Altise
- Klimaanlage Avalon Bay
- Klimaanlage TURBRO
- Klimaanlage Norpole
- Klimaanlage Cool-Space
- Klimaanlage KuulAire
- Klimaanlage BLUEPALM
- Klimaanlage Akira
- Klimaanlage Airview
- Klimaanlage Aertesi
- Klimaanlage Alberello
- Klimaanlage Kubo
- Klimaanlage Aircool
- Klimaanlage KDK
- Klimaanlage Hokkaido
- Klimaanlage Bryant
- Klimaanlage Evapolar
- Klimaanlage Liebert
- Klimaanlage Polocool
- Klimaanlage Céliera
- Klimaanlage AFINTEK
- Klimaanlage Avallon
- Klimaanlage Columbia Vac
- Klimaanlage Vostok
- Klimaanlage Quirky
- Klimaanlage KwiKool
- Klimaanlage Senville
- Klimaanlage Goodwe
- Klimaanlage Swegon
- Klimaanlage BOSFOR
- Klimaanlage Aconatic
- Klimaanlage AireMax
- Klimaanlage VänEE
- Klimaanlage Mayer
- Klimaanlage Perfect Aire
- Klimaanlage Koldfront
Neueste Bedienungsanleitung für -Kategorien-
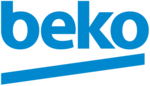
4 Dezember 2024

4 Dezember 2024

3 Dezember 2024

3 Dezember 2024

3 Dezember 2024

3 Dezember 2024
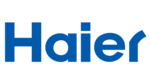
1 Dezember 2024
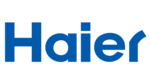
1 Dezember 2024
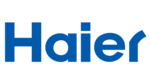
1 Dezember 2024
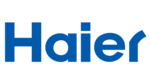
1 Dezember 2024